株式会社三友製作所様
工作機械の稼働率が20%向上!
一日の稼働状況を把握することで、作業方法の改善に結びつけるようになりました。
お客様のご紹介
株式会社三友製作所様
三友製作所様は、医療用分析機器関連製品や、電子顕微鏡関連の付属品、半導体故障解析用ツールなどの製造を行っているモノづくり企業です。
常陸太田市にある本社工場、日立市の久慈鉄工団地にある団地工場、テクノセンタの3工場を構えています。
様々な精密工作機械を使い、独自技術とノウハウで高精度な金属加工に対応し、計開発、機械加工、組立調整、出荷検査まで一貫した生産形態で多様化するニーズに応えています。
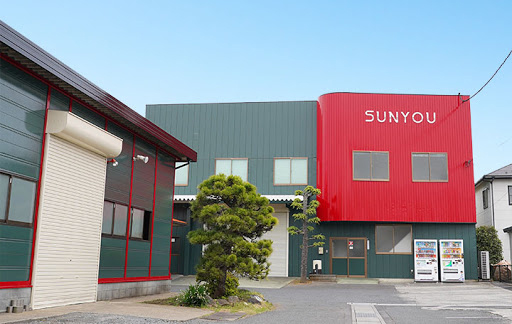
従業員数:約210名
ホームページ: http://www.sunyou-ss.co.jp/
製造業向けIoTシステムNazca Neo Linka 導入状況
導入機能
※導入時の機能と画面デザインです。最新の機能や画面デザインにつきましては、こちらをご覧ください。-
稼働監視
-
稼働管理
-
加工生産管理
-
NCプログラム通信操作
導入規模
- 導入拠点数:2工場
- 導入機械台数:合計21台
機械側との主な接続方法
- 積層表示灯(無線通信)
- オープンCNC
- 接点信号(無線通信)
- 電流信号(無線通信)
本社工場と支社工場の2つの拠点で試作・部品加工を行っており、2工場のNC工作機械をネットワークで結び、リアルタイムに全ての機械の稼働状況を把握、分析する稼働監視、稼働管理を実施。NC工作機械の実稼働データを元に機械ごとの稼働率を分析し、業務改善に役立てています。
導入前の課題
経験と勘による工作機械の稼働管理
-
工作機械の稼働状況を正確に把握できていない
-
担当オペレータの違いで生産量にばらつきがある
-
工作機械の稼働管理や生産管理を効率化したい
-
稼働率を向上したいが、現状が見えず改善方法も分からない
稼働率改善のステップ
■ 2016年10月
STEP 1 | 1台の工作機械に絞り、「Nazca Neo Linka」を導入。 |
---|---|
STEP 2 | 対象機械1台の現在の稼働状況を見える化。 |
STEP 3 | 現状の稼働状況が見えてきたことで、稼働率改善への従業員意識が向上。 |
■ 2016年11月
STEP 4 | 高稼働率に向けた対策について自主的に立案し、実施。 |
---|---|
STEP 5 | 自動取得した稼働ログを活用し、投資対効果シミュレーションを実施。 |
STEP 6 | 稼働率改善に向けて、試行錯誤を繰り返す。 |
STEP 7 | 工作機械1台において、稼働率20%向上を達成! |
■ 2016年12月~
STEP 8 | 成功した手法を工場内の他の工作機械にも展開。2工場合計21台に導入。 |
---|